Project
Complete Processing Line Replacement
Food Processing
The Problem
With market demands and supply line capacities at a high level, a client approached Agilitech to redesign and replace existing processing equipment during a limited window of 6 weeks for a shutdown.
Our Solution
Because of the time constraints and complexity of the project the Food and Beverage team at Agilitech worked with the client to perform the conceptual engineering/design, detailed engineering, procurement, and construction management to ensure an on time and on budget solution.
The Agilitech Food and Beverage team worked with the client to extensively test new processing equipment off site and choose the best new technologies. Agilitech then completely redesigned the processing line, adding state-of-the-art equipment including steam blanchers, optical sorting, high speed bagging, and PLC control systems. Agilitech developed the equipment specifications for each piece of equipment and worked with multiple vendors to customize the equipment to meet the client’s specific needs.
Agilitech created the bid packages for all contractor disciplines, held bid meetings and job walks, performed bid analysis, and selected the contractors. The Agilitech procurement group facilitated all of the requisitions to generate the purchase orders and also reviewed and approved invoicing for payment and tracked the spending for the entire project. The Agilitech purchasing group also tracked all equipment and materials to ensure everything was on-site prior to the shutdown.
The Results
Agilitech provided 7 day coverage for the entire construction period and and the entire demolition, room renovation, new equipment installation, start up, commissioning, and debugging of the system was completed 3 days ahead of schedule and on budget.
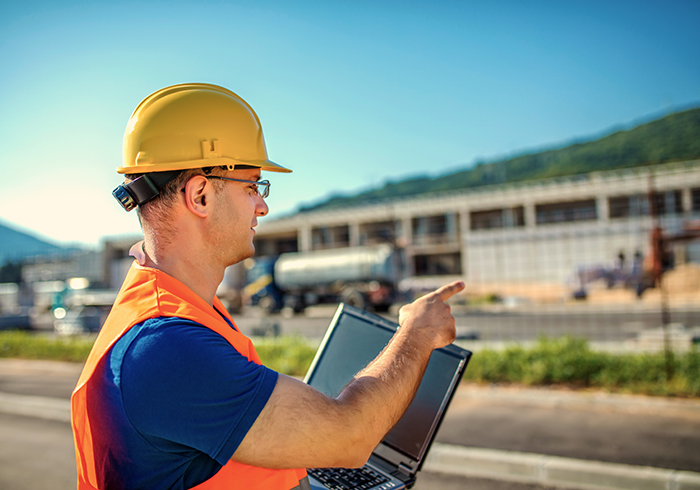
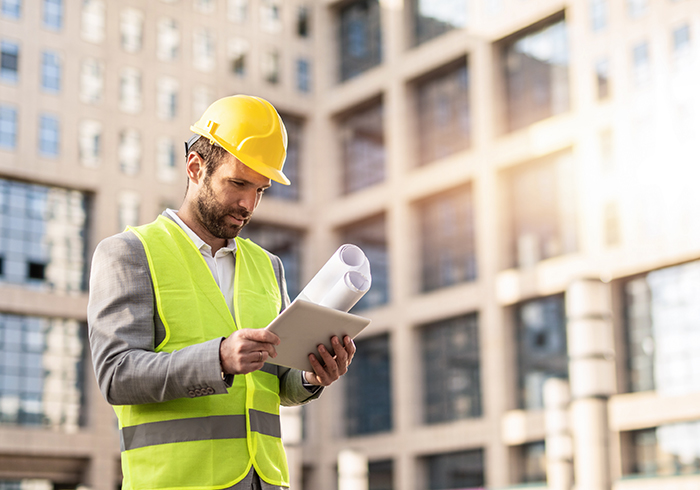