Project
Facility Design & Construction
Pistachio Hulling Facility
The Problem
A local pistachio huller wanted to increase their hulling capability. Realizing their existing facility was outdated, they approached Agilitech to design a brand-new facility. We worked with the client through a 4-year multi-phased installation.
Our Solution
The Agilitech Food and Beverage team worked with the client to determine the scope of installation through each of the different phases — using state-of-the-art 3D modeling to provide equipment layout of the processing equipment, dust collection, waste handling, as well as the plant utilities, interconnecting structure, and piping. This allowed the client to see the progression of the project through the different phases of installation, helping to ensure that each phase was installed as efficiently as possible.
Our team managed the materials balance and process flow diagrams; the part of the final configuration included (7) truck unloading pits, preclean conveyors, and hulling equipment to process and dry the nuts for conveyance to the storage silos.
Hull materials were removed with a water flume system, separated, and the excess wastewater sent to a treatment area. Dust collection and empty shell handling were upgraded and improved to handle larger volumes and greater efficiencies.
The Results
The optimized process used by the Agilitech team resulted in the new facility achieving 105% of the throughput goal and increasing processing to over 300,000 pounds an hour— while still meeting the scheduled timeframe for construction.
Thanks to the ability of the Agilitech Food and Beverage team to holistically engineer and design the facility from the ground up, this became the model for future expansions of two more hulling facilities, greatly expanding the client’s ability to process their increasing harvest needs.
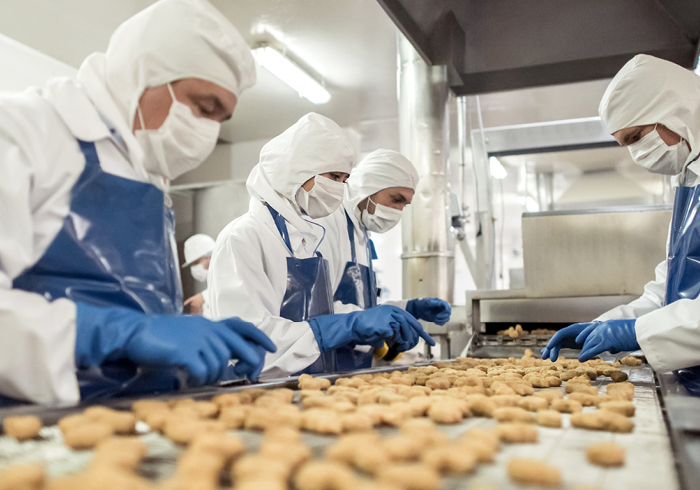
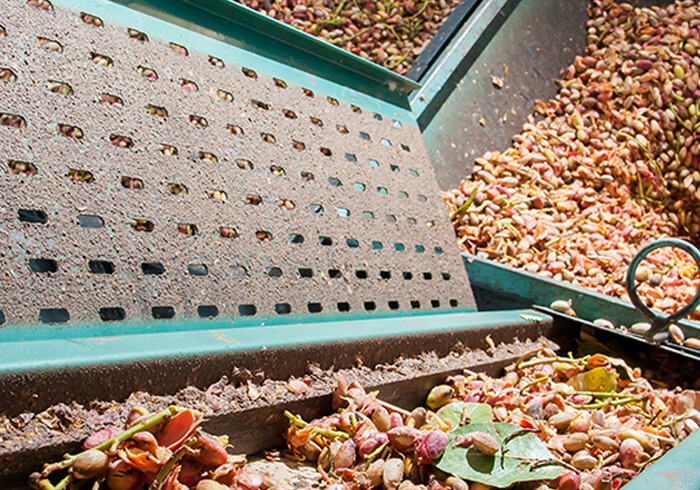